Step-by-Step Guide to Preventing Weld Undercut in Different Metals
Step-by-Step Guide to Preventing Weld Undercut in Different Metals
Blog Article
Grasping the Art of Welding: Exactly How to Prevent Undercut Welding Issues for Flawless Fabrication Results
Effectiveness and precision are paramount worldwide of welding, where also the tiniest flaw can endanger the structural stability of a produced piece. One common obstacle that welders face is damaging, a problem that can deteriorate a weld joint and lead to costly rework. By understanding the root triggers of undercut welding and carrying out reliable strategies to stop it, welders can boost their craft to brand-new levels of quality (Preventing weld undercut). In the quest of perfect manufacture results, grasping the art of welding to avoid undercut issues is not simply an ability but a requirement for those aiming for excellence in their job.
Understanding Undercut Welding

To prevent undercut welding, welders ought to make sure appropriate welding specifications, such as adjusting the existing, voltage, traveling rate, and maintaining the correct electrode angle. By recognizing the causes of undercut welding and executing precautionary actions, welders can accomplish top quality, structurally audio welds.
Reasons For Undercut in Welding
Understanding the elements that contribute to damage in welding is crucial for welders to generate high-grade, structurally sound welds. Insufficient welding present or inaccurate welding speed can additionally contribute to undercut. Comprehending these reasons and implementing correct welding strategies can aid prevent undercutting issues, ensuring strong and long lasting welds.
Techniques to stop Undercutting

To reduce the threat of undercutting in welding, welders can employ tactical welding strategies focused on improving the high quality and stability of the weld joints. One effective approach is to change the welding parameters, such as voltage, current, and travel rate, to make sure appropriate warm input and deposition. Preserving an appropriate electrode angle and ensuring constant traveling speed can likewise assist avoid undercut. Furthermore, using the right welding technique for the certain joint setup, such as weave or stringer grains, can add to minimizing damaging. Preventing weld undercut.
Utilizing back-step welding techniques and managing the weld bead profile can also aid disperse warm uniformly and decrease the threat of undercut. Regular inspection of the weld joint throughout and after welding, as well as applying quality guarantee measures, can aid in addressing and spotting undercutting issues immediately.
Value of Appropriate Welding Criteria
Choosing and preserving appropriate welding parameters is crucial for achieving effective welds with marginal flaws. Welding criteria refer to variables such as voltage, present, travel speed, electrode angle, and protecting gas flow price that directly influence the welding procedure. These specifications need to be meticulously changed based on the kind of material being welded, its density, and the welding strategy used.
Appropriate welding specifications make sure the appropriate quantity of warm is applied to melt the base steels and filler material evenly. If the specifications are set also high, it can cause too much warm input, creating burn-through, spatter, or distortion. On the various other hand, if the parameters are too reduced, insufficient blend, view it now lack of penetration, or damaging may happen.
Quality Control in Welding Operations
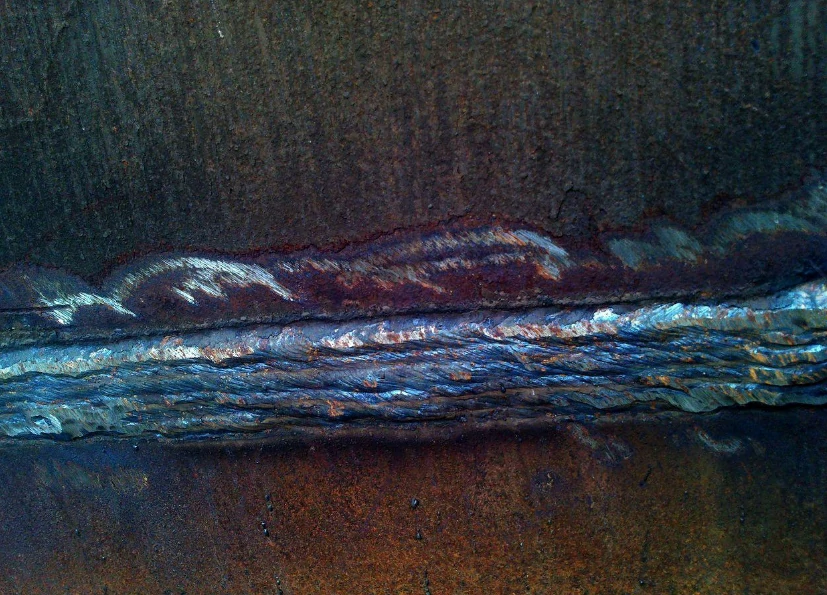
Final Thought
Finally, understanding the art of welding calls for a complete understanding of undercut welding, its reasons, and strategies to stop it. By guaranteeing appropriate welding parameters and implementing quality control practices, remarkable construction outcomes can be achieved. It is vital for welders to regularly make every effort for quality in their welding procedures to stay clear of undercut issues and create premium welds.
Undercut welding, a typical issue in welding processes, occurs when the weld steel doesn't correctly load the click for more groove and leaves a groove or anxiety along the bonded joint.To prevent undercut welding, welders should make certain correct welding criteria, such as changing the present, voltage, traveling rate, and maintaining the proper electrode angle. Inadequate welding existing or wrong welding speed can additionally contribute to damage.To alleviate the threat of undercutting in welding, welders can employ tactical welding methods intended at improving the quality and stability of the weld joints.In final thought, understanding the art of welding calls for a comprehensive understanding of undercut welding, its reasons, and methods to prevent it.
Report this page